What Is Surface Pretreatment?
Surface pretreatment is a process that involves several stages to prepare surfaces before applying any type of coating or paint. Its main objective is to remove impurities, oils, oxides, and other contaminants that affect coating adhesion while also providing protection against corrosion and environmental factors. This process not only optimizes coating adhesion but also enhances the overall resistance of the product against external agents.
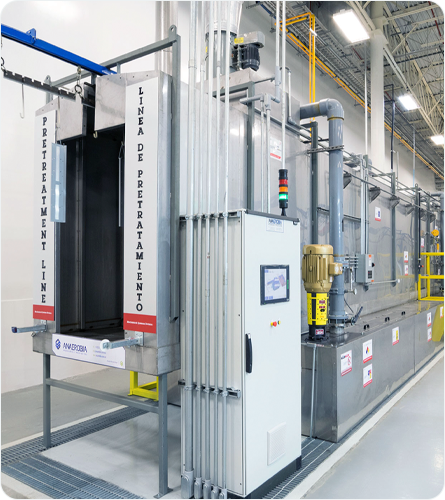
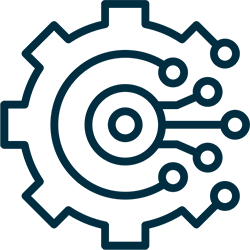
We improve global industry through
specialized engineering and advanced technology.
Why Is Surface Pretreatment Important?
Corrosion Protection:
Metals are susceptible to corrosion when exposed to moisture and oxygen. If the surface is not properly treated before painting, corrosion can form beneath the coating, leading to premature failures.
Optimal Coating Adhesion:
Surface cleaning and preparation remove oils, grease, dust, and oxides that hinder proper bonding of the paint to the surface, promoting consistent application and a high-quality finish.
Finish Longevity:
The pretreatment process ensures that the final coating is resistant and durable, which is especially important in industrial applications and extreme environments where coatings are exposed to harsh conditions.
Long-term Cost Savings:
Proper pretreatment reduces the need for repairs or repaints, resulting in improved efficiency and cost savings.
Experience: Our team has the necessary training and expertise to face the challenges of the industry.
Local Support: We are present in the country’s industrial hubs to provide close and timely assistance to our clients.
Standards: Our equipment complies with international and national regulations.
Surface Pretreatment Processes
Pretreatment can vary depending on the type of surface, coating, and final product use, typically including the following processes:
Metals are often coated with oils or greases used during the manufacturing processes. These residues can negatively affect the adhesion of paint. To remove them, degreasing solutions are used to eliminate these contaminants.
- Alkaline Degreasing: An alkaline solution is used to break down fatty bonds and remove them from the surface.
- Immersion or Spraying Degreasing: Depending on the size and shape of the metal, either an immersion system in degreasing solutions or spraying these cleaning agents may be used.
This process is used to remove oxides, scale, and other impurities through the use of acidic solutions such as phosphoric acid or sulfuric acid. This step is crucial to properly prepare the metal surface by eliminating any oxidation or surface layer that could weaken paint adhesion.
- Phosphoric Acid: Commonly used for its ability to create a passivating layer that enhances corrosion resistance.
- Sulfuric or Hydrochloric Acid: More aggressive options, used when there are heavier scale deposits or more persistent oxides.
Phosphating is a common treatment for ferrous metals that applies a phosphate layer to the surface. This layer not only improves coating adhesion but also provides an initial barrier against corrosion. There are different types of phosphating depending on the specific needs:
- Zinc Phosphating: The most common type, used to enhance corrosion resistance on most metal surfaces.
- Manganese Phosphating: Ideal for surfaces exposed to extreme wear and high temperatures.
- Iron Phosphating: While it offers less corrosion protection, it is useful in processes that require a thinner layer.
Passivation is a chemical process that follows phosphating and aims to neutralize residual chemical reactions while protecting the metal surface against corrosion during the period before paint application. It also minimizes oxide formation and enhances the durability of the coating.
To finalize the pretreatment process, the surface must be thoroughly rinsed with demineralized or deionized water to remove any residues from the previously used chemical solutions. This step is vital to prevent these residues from affecting the coating’s adhesion. Afterwards, the part is completely dried to ensure that no moisture remains on the surface.
Benefits Of Surface Pretreatment
Greater Corrosion Protection:
Our systems ensure that the treated metal is properly protected against rust and other factors that could compromise the quality of the final product.
Optimization Of Production Time:
By eliminating the risks of coating defects, repaints and reworks are minimized, resulting in more efficient production processes.
Tailored Solutions:
We understand that each project has unique needs, which is why we offer customized pretreatment systems, ensuring you achieve the best results in your production line.
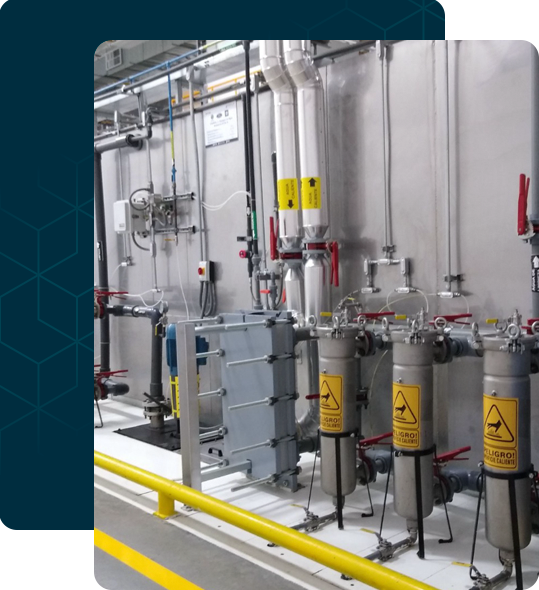
Pretreatment Solutions
We offer pretreatment solutions that optimize the preparation of your surfaces and ensure a durable and high-quality finish. Our systems are designed to maximize efficiency and ensure that your coating process is flawless.

Integrated Chemical Cleaning And Degreasing Systems:
Our cleaning and degreasing technologies are adaptable to a wide range of industrial needs, efficiently and safely removing contaminants.

Advanced Phosphating Systems:
We offer zinc phosphating and iron phosphating, tailored to the specific needs of your project. These processes ensure that metal surfaces are prepared to withstand corrosion effects and enhance coating adhesion.

Customized Passivation:
Our passivation solutions protect your metal parts during the time before painting, ensuring greater durability and long-term resistance.
Standards
Our pretreatment equipment complies with international regulations and quality and safety requirements.
We design pretreatment equipment that meets the specific needs and requirements of each client to ensure compliance with international standards (NFPA, OSHA, ETL, FM GLOBAL, ATEX, etc.).
Qualified and experienced team: Project Managers certified by IPMA.
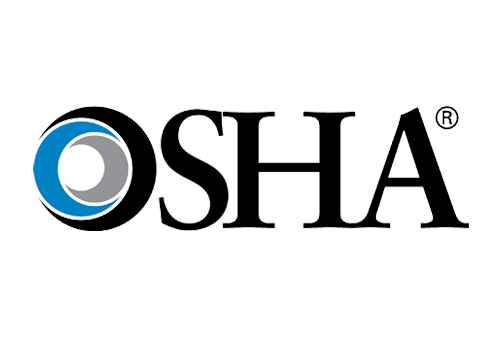
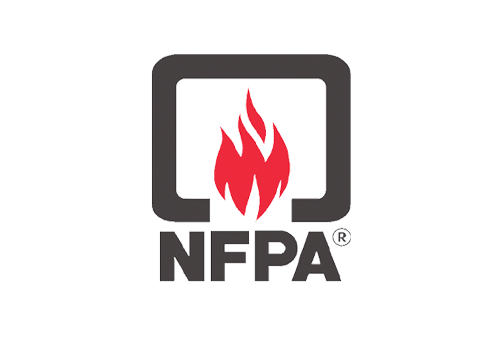
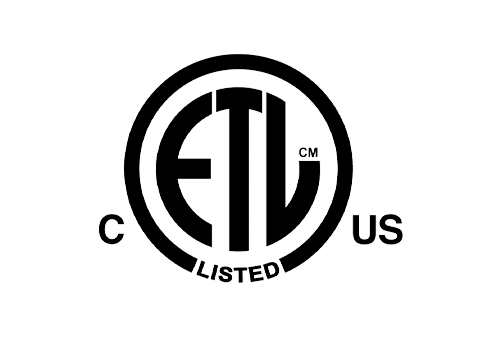
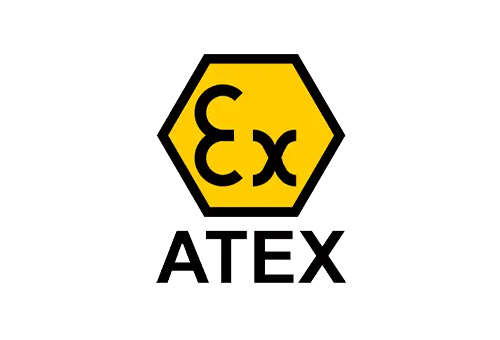
If you require additional information, please send an email.
Business Partnerships
Experience that supports us.
References
FAQ'S
Pretreatment equipment is used to prepare surfaces before coating application, removing contaminants such as grease, rust, or scale. The process includes stages like washing, rinsing, pickling, phosphating, and drying, ensuring deep cleaning that improves the effectiveness of surface treatment.
Integrated before the shot blasting system, these surface pretreatment units optimize process quality, extend the lifespan of abrasives, reduce wear, and ensure better adhesion of subsequent coatings.
Pretreatment equipment is used in industries such as automotive, aerospace, metalworking, construction, shipbuilding, home appliances, and heavy-duty transportation, where surface preparation is required prior to processes like painting or coating. These industries rely on pretreatment systems to ensure deep cleaning, improve coating adhesion, and guarantee greater durability of the components.
To choose the right pretreatment equipment, consider the type of material, production volume, the level of cleanliness required, and the type of coating you will apply. Also, evaluate whether you need a manual or automated system, the available space, and the regulations you must comply with. Choosing a reliable supplier with technical support is key to ensuring quality and efficiency in the long term.